Imagine the worst: your bustling restaurant kitchen, the heart of your operation, suddenly grinding to a halt. Your walk-in cooler, packed with fresh ingredients, is no longer holding its temperature. The reason? A broken floor, leaking precious cold air and leaving your food vulnerable to spoilage. This nightmare scenario underscores the critical role of a well-maintained commercial walk-in cooler floor, and the importance of knowing where to turn when repairs are needed.
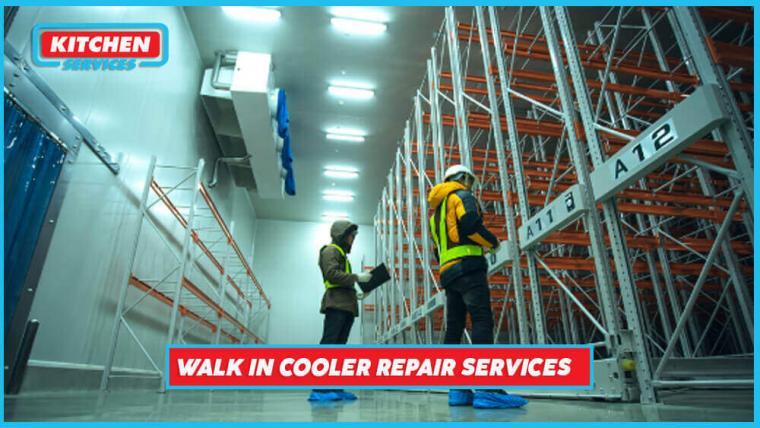
Image: kitchen.services
For food businesses, restaurants, grocery stores, and any establishment relying on commercial refrigeration, a walk-in cooler’s floor isn’t just a surface; it’s a vital part of your cold chain. A damaged floor can lead to costly food losses, regulatory violations, and operational downtime. This article delves into the world of commercial walk-in cooler floor repair ‘near me’ – from understanding the problem to finding the right solution, helping you keep your business cool and running smoothly.
Understanding the Importance of Walk-In Cooler Floor Repair
The floor of a commercial walk-in cooler plays a crucial role in maintaining refrigeration efficiency and food safety. The flooring is designed to:
- Provide a barrier against moisture and contaminants: The floor prevents water and debris from entering the refrigeration unit, keeping the environment clean and hygienic.
- Maintain refrigeration integrity: A well-sealed floor ensures consistent cold air circulation, preventing heat intrusion and energy loss.
- Support heavy loads: Commercial coolers often store heavy items, and the floor must be able to withstand constant weight and traffic.
- Enhance durability and longevity: The floor material is chosen for its resistance to wear and tear, ensuring the cooler’s lifespan and efficiency.
Common Walk-In Cooler Floor Problems
Over time, even the most robust walk-in cooler floor can succumb to wear and tear. Here are some common problems you might encounter:
1. Cracks and Splits:
Constant foot traffic, heavy equipment, and temperature fluctuations can cause cracks and splits in the floor, compromising its structural integrity. These cracks can lead to leaks, allowing warm air to enter the cooler and disrupt the refrigeration cycle.

Image: www.eztemp.net
2. Moisture Damage:
Walk-in coolers are prone to moisture buildup, especially if there are leaks or improper drainage. This moisture can seep into the floor, causing rot, mold, and even structural damage.
3. Worn-Out Insulation:
The insulation beneath the floor serves to prevent heat transfer from the outside environment. Over time, this insulation can become damaged or deteriorate, leading to decreased efficiency and higher energy bills.
4. Uneven Surfaces:
Unevenness in the floor can cause tripping hazards and make it difficult to move heavy equipment safely. Unevenness can also indicate underlying structural problems that need to be addressed.
Finding the Right Walk-In Cooler Floor Repair Solution
When it comes to fixing your commercial walk-in cooler floor, a “DIY” approach is rarely advisable. The complexities of refrigeration systems and safety regulations make it essential to rely on experienced professionals. Here’s a guide to finding the right solution:
1. Local Expertise: Search “Commercial Walk-In Cooler Floor Repair Near Me”
Start with a simple online search using keywords like “commercial walk-in cooler floor repair near me.” This will bring up local businesses specializing in refrigeration services, ensuring you have access to expertise and prompt assistance.
2. Assess the Problem:
Before contacting a repair company, take a close look at the damaged area. Note the type and extent of the damage, including any cracks, leaks, or unevenness. This information will help you communicate your needs clearly to the technician.
3. Contact a Licensed and Certified Professional:
Partnering with a licensed and certified repair company offers several advantages:
<ul>
<li><strong>Technical Expertise:</strong> Professionals have the technical knowledge and experience to diagnose the problem accurately and recommend appropriate solutions.
<li><strong>Safety Compliance:</strong> They are well-versed in industry regulations and safety standards, ensuring a safe and compliant repair process.
<li><strong>Quality Materials:</strong> They utilize high-quality materials and industry-standard repair techniques to ensure lasting results.
<li><strong>Warranty Support:</strong> Reputable companies provide warranties on their work and materials, giving you peace of mind and added protection.
</ul>
4. Discuss Repair Options and Cost:
During your initial consultation, discuss different repair options and their associated costs. The technician will recommend the most appropriate solution based on the severity of the damage and your specific needs.
5. Get a Detailed Estimate:
Request a detailed written estimate outlining the repair process, materials used, labor costs, and estimated timeline for completion. This will help you compare bids from different companies and make an informed decision.
6. Clear Communication and Transparency:
Choose a company that prioritizes open communication and transparency throughout the repair process. They should be available to answer your questions and provide updates on the repair progress.
Beyond Repair: When to Consider Replacement
While repairs can often restore the functionality of a commercial walk-in cooler floor, there are instances where replacement is the more sensible option. Here are some signs that it might be time for a new floor:
1. Extensive Damage:
If the damage to your floor is widespread or involves significant structural issues, repair may not be cost-effective or feasible.
2. Age and Wear:
If your walk-in cooler floor is nearing the end of its expected lifespan, replacement can help prevent future problems and enhance energy efficiency.
3. Inadequate Insulation:
If the insulation beneath the floor has deteriorated significantly, replacement may be necessary to restore proper refrigeration performance.
Maintenance Tips for Your Commercial Walk-In Cooler
Preventative measures are key to extending the life of your walk-in cooler floor and minimizing the need for repairs. Here are some maintenance tips:
1. Regular Cleaning and Sanitization:
Keep your cooler floor clean by regularly sweeping away debris and dirt, and sanitize it using approved solutions to prevent bacteria and mold growth.
2. Moisture Management:
Ensure proper drainage to prevent moisture buildup, and address any leaks promptly. Monitor the floor for signs of rot or mold, and remediate these issues immediately.
3. Load Distribution:
Avoid overloading the floor by distributing heavy items evenly, and consider using pallet jacks or other equipment to minimize wear and tear.
4. Professional Inspections:
Schedule regular inspections by a qualified technician to identify potential problems early and prevent them from escalating.
Commercial Walk In Cooler Floor Repair Near Me
Conclusion: Keep Your Business Cool and Profitable
A well-maintained walk-in cooler floor is essential for the success of any food-related business. By understanding the common problems, finding the right repair solution, and practicing preventive maintenance, you can keep your cooler running smoothly, minimize food waste, and protect your bottom line. If you’re experiencing issues with your walk-in cooler floor, don’t hesitate to reach out to a local professional who can provide expert advice and prompt service. Remember, a small investment in repair or preventative maintenance can save you from costly disruptions and ensure the long-term success of your business.